Introduction to Rubber Auto Parts
Rubber auto parts are integral components within the automotive industry, playing a vital role in enhancing the performance and longevity of vehicles. These parts, which encompass a wide range of components such as seals, grommets, and tires, are recognized for their flexibility, durability, and resilience under various operating conditions. The unique properties of rubber, including its ability to absorb shocks and vibrations, make it an ideal material for automotive applications, contributing significantly to vehicle comfort and safety.
The importance of selecting the right raw materials cannot be overstated when it comes to rubber auto parts. The quality of the rubber used directly impacts the efficiency and reliability of these components, affecting everything from engine performance to overall vehicle handling. Different formulations of rubber, influenced by the choice of raw materials, can alter their thermal stability and longevity, which are critical factors for automotive applications that often endure extreme temperatures and varying load conditions.
To fully comprehend the impact of rubber auto parts, one must recognize the five key raw materials that serve as the foundation for their production. These include natural rubber, synthetic rubber, carbon black, processing oils, and various additives that enhance specific qualities, such as resistance to aging and environmental factors. Each material plays a crucial role in determining the characteristics and effectiveness of rubber auto parts, making their selection a fundamental aspect of automotive manufacturing. In the subsequent sections, we will delve into each of these materials, exploring their functions and significance in the production of reliable and high-performance rubber auto components.
1.Natural Rubber (NR)
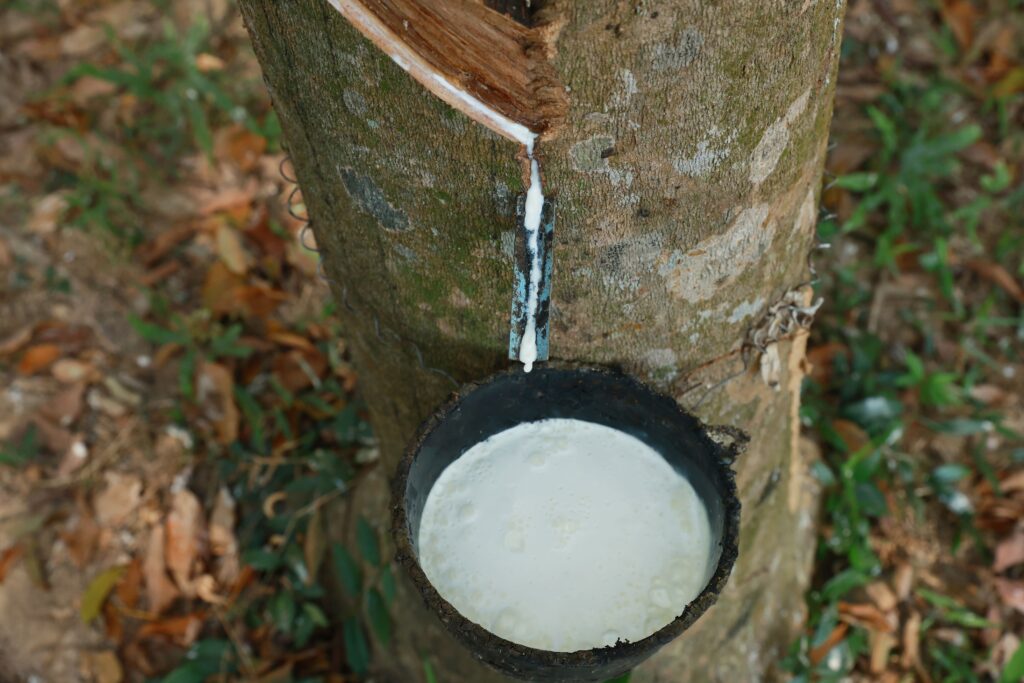
Natural rubber (NR), derived primarily from the latex of rubber trees (Hevea brasiliensis), plays a pivotal role in the production of rubber auto parts. The sourcing process involves tapping into the bark of these trees, which allows the collection of latex without causing harm to the tree itself. This sustainable practice not only supports the longevity of rubber trees but also contributes to the livelihoods of many farmers in tropical regions where these trees thrive. The latex harvested is then processed to form natural rubber, which exhibits a myriad of unique properties that make it particularly suitable for automotive applications.
One of the most notable characteristics of natural rubber is its exceptional elasticity, which allows for significant deformation when stretched while returning to its original shape. This property is essential for diverse automotive components such as seals and bushings, where flexibility and a snug fit are crucial for performance and durability. Additionally, natural rubber boasts remarkable resilience and wear resistance, making it an ideal material for parts subjected to constant movement and friction. These qualities ensure that rubber auto parts maintain their integrity over time, leading to enhanced vehicle reliability.
However, despite its many advantages, natural rubber does possess limitations. It is inherently susceptible to degradation from environmental factors, particularly ultraviolet (UV) light and ozone, which can lead to a reduction in its mechanical properties and lifespan. This vulnerability necessitates careful consideration in the manufacturing process and treatment of rubber parts, often leading to innovations in compounding and additives that mitigate these effects. Understanding these intrinsic properties and limitations of natural rubber is essential for maximizing its efficacy in automotive applications, ensuring that the engineered components continue to perform as intended over their operational life.
2.Silicone Rubber (HTV)
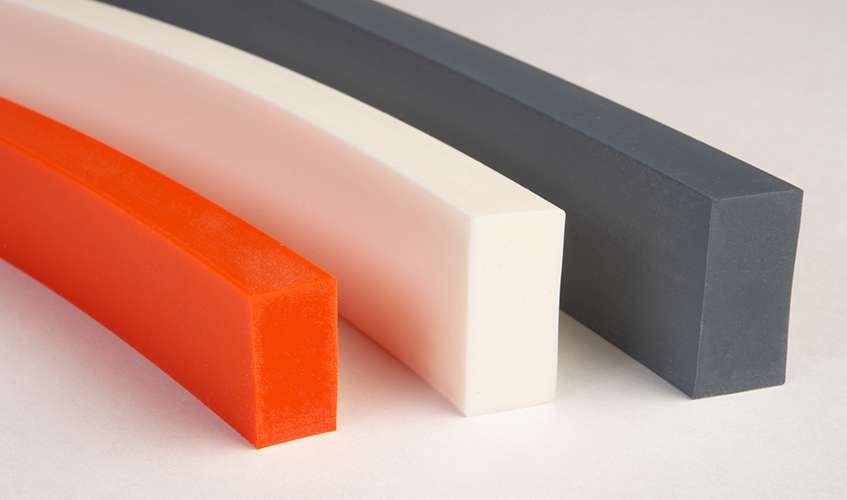
High-temperature vulcanized (HTV) silicone rubber is a specialized material renowned for its remarkable properties, particularly within the automotive sector. One of the most significant advantages of HTV silicone rubber is its extraordinary temperature resistance, capable of withstanding temperatures ranging from -60°C to 230°C. This temperature resilience makes it an ideal choice for various automotive applications where exposure to extreme temperatures is a common concern.
In addition to its impressive thermal stability, HTV silicone rubber demonstrates excellent chemical stability, which allows it to maintain its integrity when exposed to a wide array of automotive fluids and conditions. This characteristic is particularly beneficial in environments where oil, fuel, and other chemicals may be present, as it reduces the risk of degradation and ensures longevity in automotive components. Furthermore, HTV silicone rubber exhibits moisture resistance, providing additional durability in humid conditions or when combating water exposure, which is frequently encountered in automotive settings.
Another noteworthy property of HTV silicone rubber is its flexibility in cold environments. Unlike many materials that can become brittle at low temperatures, HTV retains its elasticity, making it suitable for a variety of applications that experience fluctuations in climate. Common uses of HTV silicone rubber in the automotive industry include components located in engine compartments, where heat exposure is a regular occurrence, and electrical insulation, where reliable performance is crucial to prevent failures.
Given these characteristics, HTV silicone rubber stands as a preferred material for manufacturers seeking reliable and efficient solutions for rubber auto parts. Its comprehensive set of qualities not only enhances the functionality of automotive components but also contributes significantly to vehicle safety and performance.
3.Nitrile Butadiene Rubber (NBR) and Other Rubber Types
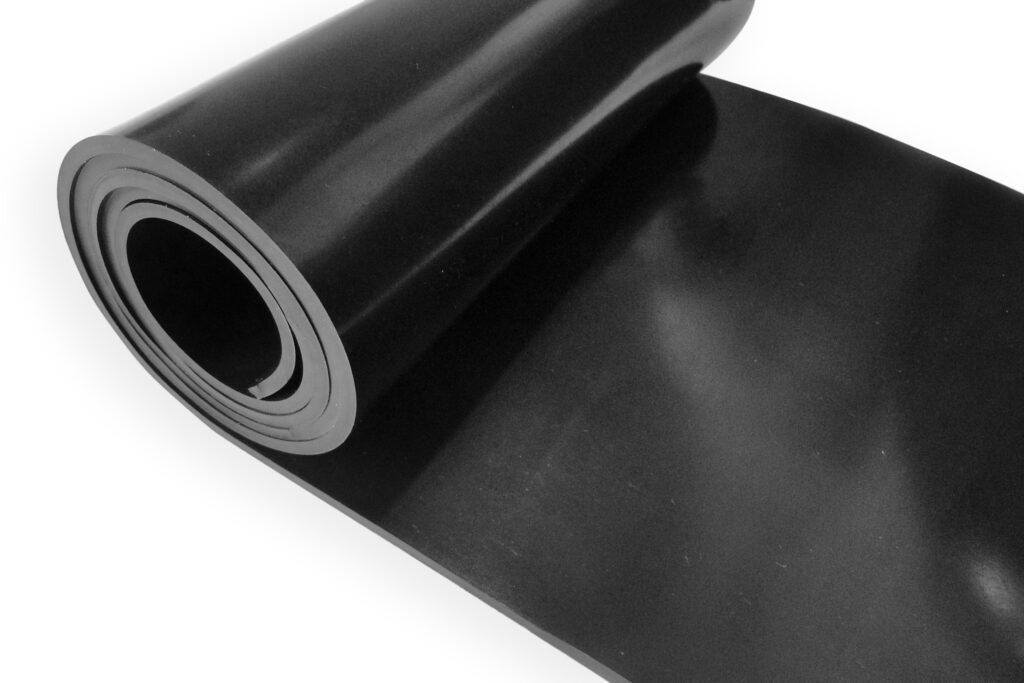
Nitrile butadiene rubber, commonly referred to as NBR, is a synthetic rubber that is particularly valued for its impressive oil and fuel resistance properties. It is composed of a combination of acrylonitrile and butadiene, which results in a material that is both durable and versatile. One of the primary attributes of NBR is its ability to maintain its integrity when exposed to extreme temperatures and aggressive chemicals, making it suitable for a variety of automotive applications. Specifically, NBR is extensively used in automotive fuel systems, gaskets, seals, and hoses, thereby ensuring reliability and performance in critical components.
In the realm of automotive engineering, the oil and fuel resistance of NBR is a significant advantage, especially in components that come into direct contact with petrol or diesel. However, while NBR excels in this area, it does exhibit some limitations, particularly in terms of ozone and weather resistance. This means that, in applications requiring high exposure to the elements, alternative rubber types may be more suitable. Exploring these alternatives, Ethylene Propylene Diene Monomer (EPDM) is another synthetic rubber used frequently in the automotive industry. EPDM is especially renowned for its outstanding resistance to weathering and temperature fluctuations, which makes it an ideal choice for seals and gaskets found in vehicles that encounter various environmental conditions.
Chloroprene rubber (CR), another noteworthy rubber type, also merits consideration in automotive applications. CR is celebrated for its balance of strength and flexibility and is resistant to oils, acids, and ozone. It is often used in applications like belts and hoses where robustness against atmospheric conditions is crucial. While each of these rubber types—NBR, EPDM, and CR—presents unique properties and benefits, the choice among them often depends on the specific requirements of the application and performance demands. The selection should always weigh the advantages of each rubber type against potential limitations to ensure optimal functionality in automotive components.
Conclusion
In conclusion, the selection of appropriate raw materials for rubber auto parts is paramount for the success and performance of automotive components. Throughout this article, we have explored various types of rubber, including natural rubber, silicone rubber, nitrile butadiene rubber, ethylene propylene diene monomer (EPDM), and chloroprene rubber. Each of these materials offers unique characteristics and benefits that can significantly impact the durability and effectiveness of auto parts.
Natural rubber, known for its excellent resilience and tensile strength, remains a popular choice for numerous applications. Silicone rubber, with its notable resistance to extreme temperatures and environmental factors, proves ideal for applications requiring longevity and reliability. Nitrile butadiene rubber stands out for its exceptional resistance to oils and fuels, making it indispensable in components exposed to such conditions. EPDM is recognized for its outstanding weather resistance, thereby ensuring long-lasting performance in outdoor applications. Finally, chloroprene rubber offers a balanced range of properties, serving as an effective choice for various automotive applications due to its versatility.
Manufacturers must carefully assess the specific requirements of their applications to select the most suitable raw materials. This consideration not only enhances the performance of the rubber auto parts but also contributes to the overall efficiency and safety of vehicles. Understanding the advantages and limitations of each type of rubber equips manufacturers with the necessary knowledge to make informed decisions. Ultimately, the right choice of raw materials translates to improved automotive performance, prolonged lifespan of components, and better value for investment, reaffirming the critical role that raw materials play in the automotive industry.